Author |
Message |
roberto
Intermediate Member Username: roberto
Post Number: 113 Registered: 3-2006
| Posted on Tuesday, May 17, 2011 - 9:45 pm: |  |
Hi Alembicians! I ve a couple of Alembics, so sometimes one of them doesnt get played for a few months. So I decided to use my Persuader 5. I find the frets buzzes..so I checked the relief, and I saw there is zero relief. So I opened the truss rod cover and loosen the bass and treble side rods , about 1/4 turn and let the wood settle for 2 days. To day I check it out and I find the treble side has some relief but the bass side seems to be not "responding"...so I opened the cover again, and loosen the bass side again...but hen I found that the bass side truss rod hexagonal screw is loose, that I can use my fingers to loosen it.. Any body have an idea what is happening and what I am supposed to do? Should I apply some heat to the truss rod cavity?or should I let some more time for the woods to move? BTW, the truss rods use to function perfectly .I tink the humidity and climate is rather 'wild' these months and it may affect the woods/ rods... Any opinions or suggestion are greatly appreciated. thanks regards /robert |
adriaan
Moderator Username: adriaan
Post Number: 2802 Registered: 6-2002
| Posted on Tuesday, May 17, 2011 - 11:29 pm: |  |
People have reported success by tuning up the bass by a whole step (E>F#, etc.) and leaving it like that for a week. Then tune down to normal pitch again, and you should have a better range of adjustment to play with. (Caveat - could have more effect on a new instrument.) |
terryc
Senior Member Username: terryc
Post Number: 1580 Registered: 11-2004
| Posted on Wednesday, May 18, 2011 - 12:38 am: |  |
roberto..DON'T APPLY ANY HEAT I would do as Adriaan says but keep a close check on it. The rule for rods are lefty loose, righty tight. Another suggestion is to loosen them totally and tighten them both at small increments and see if the neck straightens out. Again NO HEAT...only the most experienced luthiers/woodworkers know how to properly apply heat Best of luck |
roberto
Intermediate Member Username: roberto
Post Number: 114 Registered: 3-2006
| Posted on Wednesday, May 18, 2011 - 12:45 am: |  |
Adriaan, will do that right away..hope it works...thanks for the suggestion.. terryc, thanks for the warning. regards /r |
pierreyves
Senior Member Username: pierreyves
Post Number: 851 Registered: 11-2006
| Posted on Wednesday, May 18, 2011 - 6:15 am: |  |
I had the same problem with all my alembic, I do not understand why they do not truss rods that act in both directions (dual action). For those where I could not do anything, I placed a thick book of 10 cm on the 20 th box, stretched strings for a bow-shaped light, but that has changed the curvature of the neck , not the action of the truss rod. The alternative is that I did send before I bought it (from bass central) for a heatbend and there it is perfect, despite the dissatisfaction of Bass Central (spend some dollars...). For Blackwood, I asked a single truss rod with dual action. |
pierreyves
Senior Member Username: pierreyves
Post Number: 852 Registered: 11-2006
| Posted on Wednesday, May 18, 2011 - 6:18 am: |  |
I would do with book about 2 weeks in a dry place. Don't forget you can correct it also with nut and bridge adjustment, a little higher so that the neck is slightly arched |
cozmik_cowboy
Senior Member Username: cozmik_cowboy
Post Number: 958 Registered: 10-2006
| Posted on Wednesday, May 18, 2011 - 7:51 am: |  |
Oops - double post Peter (Message edited by cozmik_cowboy on May 18, 2011) |
cozmik_cowboy
Senior Member Username: cozmik_cowboy
Post Number: 959 Registered: 10-2006
| Posted on Wednesday, May 18, 2011 - 7:52 am: |  |
And triple Peter (Message edited by cozmik_cowboy on May 18, 2011) |
cozmik_cowboy
Senior Member Username: cozmik_cowboy
Post Number: 960 Registered: 10-2006
| Posted on Wednesday, May 18, 2011 - 7:52 am: |  |
Pierre-Yves, I'm not sure I understand what you're doing with the book; are you placing it between the neck & strings? Peter |
roberto
Intermediate Member Username: roberto
Post Number: 115 Registered: 3-2006
| Posted on Wednesday, May 18, 2011 - 11:02 am: |  |
pierreyves, AFAIK,Alembic's truss rods is dual action.... raising the nut would change the feel very much..I wouldnt do that I also have raised the bridge and the action to a ridiculuos level..and the buzzes wont go away..strange.. Before the problem exist, the relief is very little and the actiion is super low....without any significant buzzing... BTW, could you please explain in detail how you do it with the book? |
pierreyves
Senior Member Username: pierreyves
Post Number: 853 Registered: 11-2006
| Posted on Wednesday, May 18, 2011 - 12:47 pm: |  |
As Far As I Know (thanks to translate, I must look on google...), Alembic's truss rods have single action. All my alembic I have had (about 7) had single action except those I specifically asked for a dual action (2). Raising the nut and the bridge a little would affect the neck position and become like a bow (arc = bow ? = arch ?) in lighter of course. The string action work well in this case but you must be patient. I place the book (10 cm high) between strings and fingerboard at the 20 fret (around). I did a picture on the club some years ago but I don't remember where. Adriaan, help ?! I need to work now, I come back as soon as I can |
fc_spoiler
Senior Member Username: fc_spoiler
Post Number: 1267 Registered: 5-2006
| Posted on Wednesday, May 18, 2011 - 3:20 pm: |  |
Here you go: Too strong truss rods? |
pierreyves
Senior Member Username: pierreyves
Post Number: 855 Registered: 11-2006
| Posted on Wednesday, May 18, 2011 - 3:29 pm: |  |
Thanks FC !! here is the asked explanation:
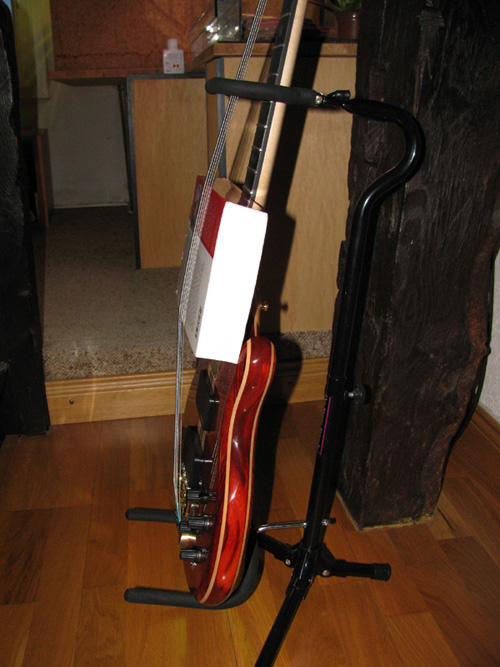 |
roberto
Intermediate Member Username: roberto
Post Number: 116 Registered: 3-2006
| Posted on Wednesday, May 18, 2011 - 5:23 pm: |  |
thanks for the picturespierreyves I will try that too! /robert |
roberto
Intermediate Member Username: roberto
Post Number: 117 Registered: 3-2006
| Posted on Tuesday, May 24, 2011 - 11:21 am: |  |
good news.. I loosen the bass side rod until it is compltely loose and can be turned by fingers,then I tune the lower 3 strings higher than pitch, even more than 1 step higher..but still not too tight to break the strings..the upper 2 strings is 1 step higher tuned.. I did use tpiereeyves 'book method" for 2 days...but I use only 2 cm thick book...and.... SOME RELIEF HAVE EXISTED ON THE BASS SIDE!!! Im really happy...Im close to selling the bass last week... but now , its again the killer sounding bass!! Adriaan, terryc and piereeyves. thanks for the suggestions best regards /r I |
daved
Junior Username: daved
Post Number: 33 Registered: 12-2002
| Posted on Tuesday, July 19, 2011 - 7:46 am: |  |
One of my Elans has been having a similar problem. The 3rd and 4th frets on the E string buzz like crazy. The bass plays perfectly everywhere else. My luthier did some adjustments and got it playable last year but now the issue has returned. Would you all recommend the "book method" in this case? |
artswork99
Moderator Username: artswork99
Post Number: 1550 Registered: 7-2007
| Posted on Tuesday, July 19, 2011 - 8:16 am: |  |
When I first received my S1 (used and stored for quite some time) there was little to no relief. I did the "book method" and it's been good to do setups since. I was careful with tension and viewed it more often than mentioned here - 2 days. How is the relief when the truss is totally loosened? Always worth a shot with some care of course. |
pierreyves
Senior Member Username: pierreyves
Post Number: 889 Registered: 11-2006
| Posted on Wednesday, July 20, 2011 - 2:19 pm: |  |
the only solution is that Alembic take into consideration what is said important from users and cionsummers of their basses. So there is never worry, it is clear that the truss rods "dual action" should be automatic, as on any other bass. Book method is a palliative method but it should never have existed. I would like to read a response or proposal from Alembic about this important subject which could strengthen consumer confidence in their products. Now I know the problem from lot of years, but not the reasons for this choice of building, I ask a single truss rod with "dual action", and it's work fine. (google translation) @Daved: your case is different because 2 cases are involved. Instead, I will raise the nut and the bridge for the string E side a little, and looks as if your neck is not twisted. (Message edited by pierreyves on July 20, 2011) |
terryc
Senior Member Username: terryc
Post Number: 1640 Registered: 11-2004
| Posted on Friday, July 22, 2011 - 6:18 am: |  |
Okay I have read this thread and attached ones and their a few things that I really cannot get a grips with this problem. I assume when Alembic insert the rods into a new bass neck they will have turned the nuts so the threads are at the halfway point when the fingerboard is installed. So therefore if you loosen them the tensions reduces, tightening the nuts increases the tension. There is no dual action, the only way you could have dual action is to have a second thread and nut at the neck end with a left hand thread. I cannot believe that a company as renowned as Alembic would use inferior or unseasoned wood when building guitar necks. Okay if you leave a unstringed bass/guitar for any length of time I guess the neck will move just as if you overtensioned the strings but we are all experienced players here and we know the do's and dont's of guitar storage etc. Placing books to pull on the strings does seem extreme to me as I have never encountered any problems with bass or guitar necks and I have had some very cheap to middle of the road to the high end Alembic I have now..I have never had a problem with neck tension or playability. It does seem a strange occurence to a very adjustable and well built instrument |
cozmik_cowboy
Senior Member Username: cozmik_cowboy
Post Number: 1024 Registered: 10-2006
| Posted on Friday, July 22, 2011 - 8:07 am: |  |
Dual actoin truss rods do exist, Terry - with one nut at one end. I have not, however, ever encountered one outside the pages of the Stew-Mac catalogue. Peter |
terryc
Senior Member Username: terryc
Post Number: 1641 Registered: 11-2004
| Posted on Friday, July 22, 2011 - 10:52 am: |  |
cozmik..thank you for that..it explains everything as far as T-rods and obviously I am not a luthier so my mechanic skill used logic(left and right thread at either end - used on the old style anti roll bars on cars) Still doesn't explain why you have to go to extreme lengths of wedging books between body and strings though. |
roberto
Intermediate Member Username: roberto
Post Number: 120 Registered: 3-2006
| Posted on Friday, July 22, 2011 - 11:23 am: |  |
I think I have to clarify again what actually is the problem. It is not about a single action or dual action truss rod..neither is saying that Alembic uses unseasoned woods. My Alembics were built in 1991. THEY HAVE BEEN FINE FOR 20 YEARS. I can loosen the truss rods and have an excessively forward bow...or i can tighten them and have a backward bow, more than enough to make the strings flat and unplayable. Its only 2 years ago that my 6 strings alembic's treble side did not give me enough relief, even though I completely loosen the hex screw .. butTHE BASS SIDE IS FINE.. and about 3 months ago, my 5 strings Alembic have the same problem..but in this case the bass side have zero relief...loosening and loosening the hex screw didnt have any effect..(TRUSS ROD FAIL??) So I did try the BOOK METHOD , using a 1 cm thick book..and tuning 1 whole step above... But I only use the book method for 2 days, cause I m afraid it may cause any unwanted wrap/swirl/bent of neck woods. But I continue storing the bass with 1 whole step above tuning for 2 weeks...and I acheive some relief on the bass side BTW, I think I read somewhere in the trouble shooting section, that heating the rods could be a remedy.. |
keith_h
Senior Member Username: keith_h
Post Number: 1699 Registered: 2-2005
| Posted on Friday, July 22, 2011 - 11:27 am: |  |
Terry, Some necks do not have enough relief when the truss rods are back off all of the way. This typically shows up when folks use light or very light gauge strings but not always. In an attempt to avoid a heat bend the idea is to increase the tension on the neck to create more relief. The books should enhance this by increasing the angle. After sitting a while the neck will settle in to the new bow. Keith |
pierreyves
Senior Member Username: pierreyves
Post Number: 893 Registered: 11-2006
| Posted on Friday, July 22, 2011 - 11:31 am: |  |
Mica ? |
terryc
Senior Member Username: terryc
Post Number: 1642 Registered: 11-2004
| Posted on Saturday, July 23, 2011 - 12:18 pm: |  |
Okay I know abou the relief bit but surely Alembic check all this at their quality control end?? I mean some customers have waited a long time for their basses and surely this would have been apparent before sending them out?? Without attaching blame..are they stored correctly whilst not in use, and how should they be stored for a long period. I was told that if not in use for a short period of time then place them on a stand out of direct sunlight and in a relatively cool place(not too cold though) Longer storage is to place in the case and store the case out of sunlight I think someone on here said under the bed(if there enough clearance of course) As I said I have had some really cheap basses but never encountered this problem at all |
dfung60
Senior Member Username: dfung60
Post Number: 500 Registered: 5-2002
| Posted on Sunday, July 24, 2011 - 3:55 pm: |  |
The thing to remember about the neck is that it's made of wood, which is a natural product where it's reaction to the environment is not totally predictable. This was true when Alembic built your basses and continues to be true in your environment as well. The common practice in making guitar necks is that you assemble the neck, then shape and level the fingerboard and then the fret tops so that they're dead flat when the instrument is unstrung. When you string the bass to pitch, this will pull the neck into a bowed shape, then you adjust the truss rod to counteract most of that bow. If everything works out right, then the relief should be just right to prevent buzzes and give you can adjust the action to fit your playing style. "Everything working out alright" includes having the wood deform evenly along it's length and making sure you've properly designed the truss rod to provide support where your neck needs it. On top of all this, wood may respond to humidity and temperature in ways that may change how it behaves - it may become stiffer or more flexy, or might do either irregularly along it's length. Over time, it may gradually change as a result of aging, too. When your instrument was made, the setup was done by a highly skilled luthier (probably James for many of us!). They can do a perfect leveling of the fingerboard and frets, but they are doing this in the environment of the shop. There's no way that they can anticipate what the climate or conditions will be like when it gets to you and no way to tell the wood not to be reactive. If you had two basses, never had troubles, then both basses developed the same action problems at the same time, then I'd guess the climate is a factor - probably that it's been drier or hotter than in the past. If the weather changes (with the seasons or if this has been an unusual year), then you may see the problem disappear on it's own. Or if this is the effect of aging or an ongoing change in your environment, then perhaps you'll need to have some work done. You could send it back to Alembic, but you risk facing the same problem - they can make it perfect, even to your hands in Santa Rosa, but it might not be right when you take it home. So, if this is a persistent problem, you may want to see if you can find a local tech who can work on this. If you're seeing this problem, then others may be seeing it as well. I don't think this is likely to be an issue of quality control, because the "quality" that changed is probably your environment, not the instrument. Now, you do bring up a very good point- why is this happening on my Alembic when it's not happening on a $500 Fender or Ibanez? Part of it may be that the wood just wasn't as sensitive to humidity changes. Every piece of wood really is different, whether it is going into a $500 or $5000 bass. You may find cheap basses that aren't affected and other ones that have much more change, or some other Alembic that isn't affected. One thing that may also be a factor is that different instruments may have a wider range of truss rod adjustment. Having a wider range of truss rod effect may help improve the yield of sellable necks for a big builder. But in your Alembic you've paid a lot of money for fine tonewoods, and I think it's good design if the trussrods aren't intended to carry the bulk of the neck tension - that's your sound, you know! For those of you that are familiar with Modulus instruments, the original design is an all-graphite monocoque (hollow tube) with no truss rod, and no way to adjust action other than through (expensive) fretwork. This wasn't an error in the design, it was quite intentional on the part of the company founder, Geoff Gould. He really believed in the audio benefits of having graphite bear all the structural tension and didn't want to dilute that with a truss rod. In later years, Modulus has come to adopt a truss rod for fine tuning playing action, although the adjustment range is limited because of the strength of the neck. Alembic necks are generally quite strong and stiff because of the laminated construction, so I think you may be seeing a little less adjustment range there as well. There are dual action truss rods out there, but you should be able to get good results with either type. The tension of the strings always makes the neck bow, and the truss rod counteracts that. In a normal truss rod, the threaded adjuster that you turn is pushing against a block of metal attached to the neck. If you had a double action truss rod, it actually traps this block of metal on both sides, so loosening the nut actively decompresses the rod. But the tension from the strings is higher than the truss rod nut anyway, so loosening the truss rod should cause more bow in any case. All that the dual action rod buys you is that you won't loosen the adjuster off the threaded end of the rod. This is kind of like the way tuners work - a double action truss rod could push the action slightly higher, but it probably won't hold this position if the strings aren't providing the bow, just as your tuning won't be right if you tune down to pitch. Sorry for the long rant. I'm not sure where you are, but it's hard not to notice this thread popped up again when the Midwest and East Coast of the US are getting a record baking (I did see that this thread started months ago though). If this isn't the result of today's weather, it may be time for a visit to the shop. After 20 years, it would only be surprising if the wood characteristics HADN'T changed at least a little. When you read about a Stradivarius violin, it's not unusual to see what appears to be major surgery over the years. Of course, you want to maintain such a rare instrument in as original a form as possible, but it's also recognized that this sort of work is expected on any instrument. David Fung |
bigredbass
Senior Member Username: bigredbass
Post Number: 1737 Registered: 9-2002
| Posted on Sunday, July 24, 2011 - 4:58 pm: |  |
And so much of this is down to how you play. In the early days, I frammed away on my basses with Fender Heavy picks (the big 155-style triangles, they can double as Throwing Stars in tight spots . . ), you could probably put two quarters between my strings and the fingerboard, and hey, it didn't buzz ! What did I know? As I grew up and began to find a style and played more and more with my fingers, I began to want a little easier time of it. Had techs here and there set them up, it was better. Then when I got my first Alembic, all of my imperfections were served up on a plate (damn hi-fi pickups!). Since the BRB was a long-scale Series shape axe, it really begged to be set up properly. It dawned on me that between the adjustable nut and the one-piece bridge, NOW was the time to teach myself. And off (or sometimes OOF) I went . . . Ive been around LOTS of basses and I'm utterly convinced that these leave me nothing to question about their 'quality control'. I'm also totally convinced that the multiple laminations plus the ebony fingerboard are as structurally solid as one can get without going to composites, etc. And they only use wood that's been time and humidity stabilized before it's ever touched to begin a new bass. I'm well satisfied that they've done everything smart and possible to build as long lasting a neck as possible. Now having said that, wood can do things over time that no one can control. Frets can wear or unseat, you get the occasional shrinking fingerboard where the fret ends begin to poke out, these things just happen, whether it's a Squier or a Ritter. And even the best prepared and aged wood can pull pranks after it's sawed, glued, sanded and painted into a guitar. And even if none of that happens, remember that the difference between 'feels great' and 'it's buzzing like mad' is only a few thousandths of an inch in relief, or half-turn in the bridge height, or a quarter-turn in the truss rod. I taught myself setup so I could adjust to a set of numbers to get my basses to exactly where I wanted them. Now that I've got those numbers, I know when it's right and I know when it's going away when the measurements come back wrong. So, with that . . . 1) They're re-strung with exactly the same strings every time, always tuned 2) They store in their case leaned against the wall, big end down, obviously 3) They are never kept anywhere I wouldn't be comfortable (no car trunks, etc.) . . . so I really don't have set-up problems. Down the road they may need frets, or a fret dressing, but that's to be expected. Over time, wood will settle into a stability, but I must admit I respect it enough to not provoke it into mischief. As always, my fave Mica quote, "sooner or later, it will realize it's not a tree anymore". J o e y (Ed. Note: I'm as long-winded, but not nearly so eloquent as David Fung) |
terryc
Senior Member Username: terryc
Post Number: 1645 Registered: 11-2004
| Posted on Monday, July 25, 2011 - 3:48 am: |  |
Joey..yep your setup instructions are copied and pasted into one of my info files. I have never paid for any setups and have done quite a few for my son's friends to which they all are very appreciative(I never charge them, they always get me a pack of beers) |
|