Author |
Message |
jalevinemd
Senior Member Username: jalevinemd
Post Number: 983 Registered: 12-2003
| Posted on Wednesday, April 22, 2015 - 7:00 pm: |  |
Series 1 Guitar Nice guitar, but I don't understand where people get their asking prices from. Puff…puff..pass. |
sonofa_lembic
Member Username: sonofa_lembic
Post Number: 86 Registered: 5-2014
| Posted on Friday, July 31, 2015 - 3:25 pm: |  |
Way too expensive, and look at the massive crack in the middle of the fingerboard! |
lbpesq
Senior Member Username: lbpesq
Post Number: 6185 Registered: 7-2004
| Posted on Friday, July 31, 2015 - 7:00 pm: |  |
I don't see the crack, maybe because I'm looking on my iPad. Where on the fingerboard is it? Bill, tgo |
elwoodblue
Senior Member Username: elwoodblue
Post Number: 1665 Registered: 6-2002
| Posted on Friday, July 31, 2015 - 7:37 pm: |  |
I had a couple minutes...it looks like it should have been oiled a long time ago.
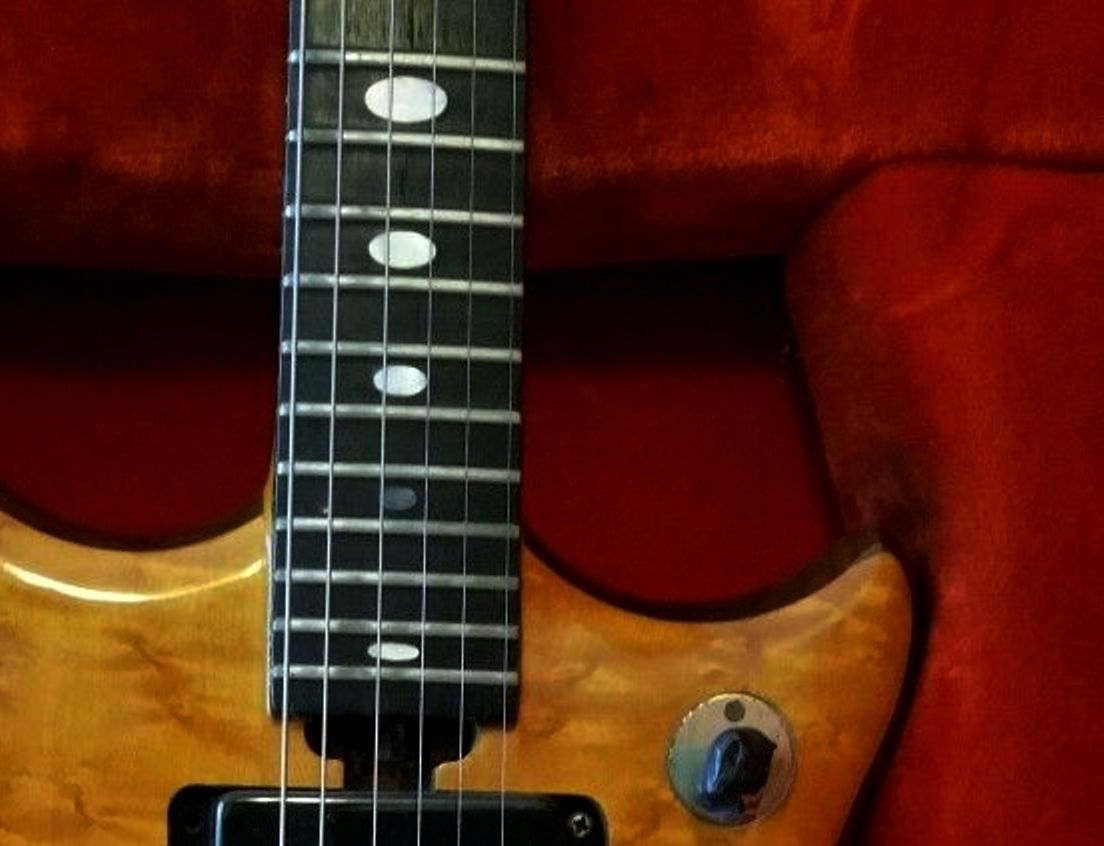 |
lbpesq
Senior Member Username: lbpesq
Post Number: 6187 Registered: 7-2004
| Posted on Saturday, August 01, 2015 - 10:24 am: |  |
Thanks, Elwoodblue. Now I see it. Too bad! It amazes me how many old guitars I have obtained that seem to have never had their fret-boards oiled for decades. When I do get one of those, boy do they suck up the lemon oil in a matter of seconds! Bill, tgo |
gtrguy
Senior Member Username: gtrguy
Post Number: 903 Registered: 9-2004
| Posted on Saturday, August 01, 2015 - 12:14 pm: |  |
Why would oiling them keep them from cracking? Thanks |
enzo
Senior Member Username: enzo
Post Number: 509 Registered: 4-2009
| Posted on Saturday, August 01, 2015 - 8:28 pm: |  |
I'm not the most qualified guy in these things but I guess it's because, being the fretboard usually the only untreated wooden part of the instrument, when it contracts and expands and there's not enough moisture, it cracks. |
ed_zeppelin
Junior Username: ed_zeppelin
Post Number: 17 Registered: 2-2010
| Posted on Sunday, August 02, 2015 - 12:07 am: |  |
I've been an instrument repairman (primarily acoustic) since the 80s, and all I've learned is that trees are like people. Each is unique. A tree can have a hard year or two, and it'll show someplace. Wood grain is a record, remember. Cells attach end to end like crazy so the tree can climb to the sky. Side to side, not so much. And it's dried. (Kinda.) I taught at a Summer guitar clinic in New England, and midway through it one of those horrendous, 110 degree, 99% humility heat waves hit. I took a straightedge around and asked if I could lay it across the bottom bout of acoustic guitars, just behind and parallel to the bridge. Before lunch, most were dead flat or reasonably close. By late afternoon there was a good half-inch of clearance on the edges. All a luthier can do is mitigate, balance, compromise. If any competent repairman is honest, they'll admit that in at least some cases, we have no idea what happened. Wood twists, warps, swells, misbehaves. Sure, using a stand helps (MF has those wonderful self- locking "Auto Grab" Hercules stands for $28! http://www.musiciansfriend.com/accessories/hercules-stands-single-guitar-stand-with-folding-yoke?rNtt=Hercules&index=3 ) and rub in lemon oil on the fingerboard now and then, but stuff just happens sometimes. Check out the cleats in this 365 year old Venetian double bass, from @1650 http://www.contrabass.co.uk/images/instruments/2790/pre_restoration/10-front-inside.jpg each represents a failure of some sort. Another view: http://www.contrabass.co.uk/images/instruments/2790/pre_restoration/14-bass_ribs.jpg Here's the history: http://www.contrabass.co.uk/2790.htm Stuff just happens sometimes. I can't imagine the wood cracking down the center of the Alembic's fingerboard without the truss rod channel being involved, somehow, but that's just a wild guess. If it was hneer to uniform dryness in the wood, ii seems like it would have shown up somewhere else as well. It's an easy fix, fortunately. |
ed_zeppelin
Junior Username: ed_zeppelin
Post Number: 18 Registered: 2-2010
| Posted on Sunday, August 02, 2015 - 12:10 am: |  |
I've been an instrument repairman (primarily acoustic) since the 80s, and all I've learned is that trees are like people. Each is unique. A tree can have a hard year or two, and it'll show someplace. Wood grain is a record, remember. Cells attach end to end like crazy so the tree can climb to the sky. Side to side, not so much. And it's dried. (Kinda.) I taught at a Summer guitar clinic in New England, and midway through it one of those horrendous, 110 degree, 99% humility heat waves hit. I took a straightedge around and asked if I could lay it across the bottom bout of acoustic guitars, just behind and parallel to the bridge. Before lunch, most were dead flat or reasonably close. By late afternoon there was a good half-inch of clearance on the edges. All a luthier can do is mitigate, balance, compromise. If any competent repairman is honest, they'll admit that in at least some cases, we have no idea what happened. Wood twists, warps, swells, misbehaves. Sure, using a stand helps (MF has those wonderful self- locking "Auto Grab" Hercules stands for $28! http://www.musiciansfriend.com/accessories/hercules-stands-single-guitar-stand-with-folding-yoke?rNtt=Hercules&index=3 ) and rub in lemon oil on the fingerboard now and then, but stuff just happens sometimes. Check out the cleats in this 365 year old Venetian double bass, from @1650 http://www.contrabass.co.uk/images/instruments/2790/pre_restoration/10-front-inside.jpg each represents a failure of some sort. Another view: http://www.contrabass.co.uk/images/instruments/2790/pre_restoration/14-bass_ribs.jpg Here's the history: http://www.contrabass.co.uk/2790.htm Stuff just happens sometimes. I can't imagine the wood cracking down the center of the Alembic's fingerboard without the truss rod channel being involved, somehow, but that's just a wild guess. It's an easy fix, fortunately. |
lbpesq
Senior Member Username: lbpesq
Post Number: 6190 Registered: 7-2004
| Posted on Sunday, August 02, 2015 - 9:47 am: |  |
My understanding is that natural oils in the wood dry out and leave tiny, (like molecular size), voids in the wood. The lemon oil has molecular components that fill these voids - or at least I seem to remember Mica posting something along those lines. And, of course, it smells good! Bill, tgo |
lbpesq
Senior Member Username: lbpesq
Post Number: 6191 Registered: 7-2004
| Posted on Sunday, August 02, 2015 - 10:01 am: |  |
Found it. Mica, from 2005: "Our thought on the finish of a fingerboard is that Ebony is very stong and durable all on its own and we prefer it in its natural state. It also has a wonderful touch. In my experience, both pure linseed oil and pure tung oil rarely fully harden. That bothers me, but perhaps I'm just very sensitive. Polymerized oils do fully harden, but that too changes the touch. I've even heard of folks using Thompson's Water Seal on fingerboards. As the larger organic molecules, like the heavy turpines, evaporate from the Ebony, a pure lemon oil (which is rich in these compounds) penetrates just enough to replenish these and impede cracking. Oils also help dissolve the gunk that accumulates on well-played fingerboards. Eduardo once suggested lighter fluid (naptha) is commonly used in Mexico for cleaning fingerboards so I tried it. It evaporates pretty quickly, and the board isn't super rich black when done, but it does seem clean. After some pure lemon oil, it looked great. It's true that some people never oil their fingerboards and never have any troubles with cracking. We repair far fewer cracks on fingerboards where the owner has cared for it with a good quality oil. We use a fairly thick piece of Ebony, and it can take levelling and refretting several times if done by a carfeul repairperson. The fingerboard is not viewed as a permanent part of the instrument. Hopefully eventually someone will play the instrument enough that it requires replacing after several refrets. I think that means we did a good job, worthy of a player spending time making that much music on it. You have to balance how much you want to preserve the board to the way it feels when you play it." |
jazzyvee
Senior Member Username: jazzyvee
Post Number: 4603 Registered: 6-2002
| Posted on Sunday, August 02, 2015 - 4:26 pm: |  |
I just do mine about twice a year and it seems to stay looking lovely and black. I also think that guitar is a tad overpriced but if he finds the right buyer it may indeed fetch that price. |
ed_zeppelin
Junior Username: ed_zeppelin
Post Number: 19 Registered: 2-2010
| Posted on Sunday, August 02, 2015 - 10:58 pm: |  |
From an interview with Doug Irwin about Jerry Garcia's guitars: "DI: I used a lot of Schaller stuff, exclusively Schaller tuning stuff on all of Jerry's guitars. SQ: Any particular model number? DI: Well the M6, M6G because I got the gold-plated. Jerry had an unusual body chemistry. Of all the people that I've worked on guitars for, I've worked on guitars for a lot of people, Jerry had the most corrosive sweat. SQ: What effect did that have? DI: Actually it was kind of interesting because he can eat through chrome nickel plating in three weeks. I'm not kidding you, this is like what bumpers of cars are made out of you know, it's resistant. But gold, he didn't react to, and it lasted a long time. SQ: I wonder what caused that to happen? DI: Well, just the fact that human beings are all similar, but we're all different. Body chemistry from individual to individual varies quite a bit. The gold tuning gear was really, I mean that's one of the reason that I used Shallers because they really do incredible plating and stuff like that. When they do gold plating on something, they don't fool around. The gold really lasts a long time, they use such a nice shade of gold, too. There's 21 colors of gold in natural shades. But Germans are really good at making metal stuff. It's kind of the only thing they had to work with. They're sitting on top of the iron triangle and it's not a good farming region, so what do you do? ..." http://dozin.com/dougirwin/interviewpg3.html As a repairman, I can vouch for the fact that a lot of people oil their fingerboards every time they play. it's a lot more widespread than you'd think. The bassist Billy Sheehan has to wear TWO wristbands on each hand to keep the flow of grease and corruption in check. I have a small plastic box filled with the desiccated grease and finger scum scraped off Joe Walsh's fingerboards from a couple of refret jobs we did for him. (The glamorous part of the job.) |
lbpesq
Senior Member Username: lbpesq
Post Number: 6192 Registered: 7-2004
| Posted on Sunday, August 02, 2015 - 11:55 pm: |  |
While Alembic has produced a very limited output of instruments, compared to many other manufacturers, they've undoubtedly built and repaired a heck of a lot more instruments than Irwin ever did. How many Irwin instruments, other than Jerry's (which did not include Wolf, a true Alembic), and Phil's bass have you seen? I strongly suspect that Irwin built a relatively modest number of instruments. That would explain why they are rarely seen. Personally, I believe Irwin's reputation is built largely upon his association with Jerry rather than upon his experience and the instruments he built. I'll take Mica/Alembic's advice over Irwin's any day. And I suspect the components of human finger oil are quite different from lemon oil and wouldn't nourish the wood in the same manner. Bill, tgo (Message edited by Lbpesq on August 02, 2015) |
jazzyvee
Senior Member Username: jazzyvee
Post Number: 4604 Registered: 6-2002
| Posted on Monday, August 03, 2015 - 12:37 am: |  |
I guess I have something in common with Gerry then. I didn't realise until 92 when I first went on tour in the states that my finger sweat was corrosive. I was changing strings every other gig as the plating was completely removed of the strings and they would corrode and break where I'd been in contact with it. I tried all the strings recommended by the guitar stores in places we visited. Obviously I wasn't working hard enough here in the uk for that to be a problem. Anyway years later when I toured there again I still had the same problem and visited GC in LA and they recommended Elixir coated strings.... bingo problem solved. They even gave me huge discount because I was on tour so I bought a couple of boxes. Interestingly i've not had the same problem yet playing bass. That said I still lemon oil my guitars fairly regularly. Actually my strat has an ebony board and I never knew it should be oiled at all until I got an alembic and read here on the forum about caring for ebony fingerboards. That guitar doesn't have any splitting problems and it had been my only gigging guitar for about 10yrs. |
ed_zeppelin
Junior Username: ed_zeppelin
Post Number: 20 Registered: 2-2010
| Posted on Monday, August 03, 2015 - 12:47 am: |  |
I apologize if my post offended anyone. After decades of scraping other people's funk off fingerboards, the topic makes me shudder like being tased in the shower. The reason I quoted that segment of Doug Irwin's interview was simply because it's one of the only times the topic corrosive digital effluvience has ever come up, and I thought it was rather endearing that Jerry Garcia was just like the rest of us - a point he seems to have steadfastly maintained his whole life, from what I understand. I didn't mean to disparage anyone. I just thought it was amusing. |
mica
Moderator Username: mica
Post Number: 8591 Registered: 6-2000
| Posted on Monday, August 03, 2015 - 7:55 am: |  |
Forest, I imagine we've both seen some crazy gunk on fingerboards. Years of sweat, skin cells, dust, smoke particulate, animal hair, spilled drinks... it can be gross for sure. But that crud does clean off, and lo! who knew there was such a nice Macassar Ebony board under there?! We deal with the corrosive sweat issue regularly. It's one of the reasons that for YEARS we installed only chrome tuners on instruments, even with brass hardware. In 25 years, they still look new, while the gold usually looks bubbled if there is a reaction or it simply just wears off. With the plating, what really happens is the coating isn't 100%, there are small pores that your sweat can still penetrate. When the manufacturer does it right, chrome and gold will be be most resistant. That's because they have a substrate layer of nickel on the brass. Usually, a pore in the gold plating won't line up exactly with a pore on the nickel plating and there for your sweat will never get down to the brass and start reacting. You can't tell what the under layer is (or even if it's there) by looking at it. It's only after the brass starts corroding that you can see the result. We had a gold plater that used a copper layer under the gold. Well, that corroded pretty fast! |
ed_zeppelin
Junior Username: ed_zeppelin
Post Number: 21 Registered: 2-2010
| Posted on Monday, August 03, 2015 - 11:58 am: |  |
I have one of these for each instrument: http://thestringcleaner.com/ I use it when putting the instrument away, and just leave it on. Then I give it a quick zip up the strings before playing. My strings stay bright a lot longer now, and I can't imagine an easier way to maintain strings. By the way, I always ask the bartender or waitress if I can have a clean bar-towel or two. They're fantastic for keeping your stuff clean and spanky. And they're free. Always an attractive quality. The Dopera brothers (that's how they spelled their surname) were family friends, so I got to spend a lot of time in their Dobro factory when I was a kid. Here's the Dobro Ed Dopera made as a gift to my dad:
Ed believed that ammonia from Uric acid was the cause of corrosion, so the earliest Dobros were made of a special corrosion resistant "bell brass" from Czechoslovakia, which was then plated with nickel and/or chrome. (Ed still had a stash from the 1930s he used for special instruments, like my dad's.) Fingerboards were "red bean wood" or ebony. (Most postwar models had rosewood fingerboards.) as a finishing touch the fingerboards and "armrest" area of metal-bodied roundneck Dobros were given a thin coat of bowling alley wax (I kid you not). If I can quit blabbering down memory lane here and get back to the topic (my wife, the Foghorn, says I should wear a sign that says: "don't get me started"), the crack in the fingerboard of the Series 1 guitar that this thread was ostensibly about was probably not caused by drying out, in my astoundingly humble opinion. (Though of course that could be a factor.) Look at where it is: a small area in the middle of the fingerboard, only an inch or two long. Most fingerboard cracks I've seen were near the ends of the fingerboard, especially at the body end. The nut usually keeps everything together on the other end. Since the only thing going on underneath that section of fingerboard is the trussrod channel (I don't know if dual truss rods were standard then) that seems a likely culprit. I'll bet somebody went; "ooh, something bright and shiny! I'll just stick a socket on that sucker and crank it until I hear a cracking sound!" |
mica
Moderator Username: mica
Post Number: 8594 Registered: 6-2000
| Posted on Tuesday, August 04, 2015 - 2:35 pm: |  |
I'd be surprised if the truss rod channel were involved. For one thing, the fingerboard is glued to a veneer of Walnut, so you'd have to crack a glue joint too. A crack is most common at the ends of course (though I don't think the nut helps shield against water vapor coming or going, as it's not quite THAT close to the fingerboard and it's not glued to the end). I've seen cracks all over the fingerboard, starting anywhere. They will continue to grow until arrested. This one happens to be in the middle. Anyway, it's probably possible to fix it, and in the absolute worst of all cases, fingerboards can be replaced  |
ed_zeppelin
Junior Username: ed_zeppelin
Post Number: 23 Registered: 2-2010
| Posted on Tuesday, August 04, 2015 - 4:10 pm: |  |
Thank you so much for taking the time to clarify. >>> I've seen cracks all over the fingerboard, starting anywhere. <<< Exactly. I thought of two words, one of which is "happens." I saw Dan Erlewine fix one of those unexplainable fingerboard cracks in about thirty seconds, in a demo at the ASIA symposium. http://asiartisans.org/content/ The frets were off in that area. He squirted a thin line of superglue in the crack, delicately ran a fine file against the grain so the wood-powder (?) filled it, hit it with activator and quickly dressed the fretboard. Boom, done. You absolutely could not tell where the crack had been. I love playing "Guitar CGI, " trying to figure out whodunit. Maybe it's because of my name. Oh what the hey. Might as well tell you my favorite story about it. I was working at the world's largest used instrument retailer in New Hampshire during a record breaking Winter. It had been over a month since the thermometer went above zero. Part of my job was RTM (return to manufacturer) and suddenly we were hit with a mountain of guitars with finish problems, especially out-of-control checking. The owner of the company was furious, because it was tens of thousands of dollars in new guitars and the companies were understandably reluctant to replace them. The owner had placed his 16 year old son in charge of the warehouse, promoting the guy who had ran it for over twenty years to manager of one of the stores. The owner's son had cranked the heat in the warehouse. He wanted to show his old man what a good job he was doing, so when the trucks delivered the guitars, the first thing the kid did was open the (below-zero) cases and take the guitars out to inspect them personally. The owner said that he walked in just as the kid opened the case of an expensive hollowbody and pulled it out.. He said you could HEAR the finish cracking, and his son said; "there it is again! What keeps causing that, dad?" |
elwoodblue
Senior Member Username: elwoodblue
Post Number: 1667 Registered: 6-2002
| Posted on Tuesday, August 04, 2015 - 4:25 pm: |  |
I hear that sound when I pull french bread from the oven,only then it's a sign of things properly done. Goes to show...knowledge IS power Thanks for the story and the Dan E. tip! |
jalevinemd
Senior Member Username: jalevinemd
Post Number: 1044 Registered: 12-2003
| Posted on Tuesday, August 04, 2015 - 4:35 pm: |  |
What upsets me is that (as is all too often) the seller fails to mention this "little" detail. I looked at these pictures several times and didn't notice the crack until Trevor brought it to my attention. If I bought a guitar on ebay only to find out that the fingerboard needed to be replaced, I'd be pissed beyond belief. Because then you have to factor in the cost of shipping to and from Alembic, the cost of the work to be done and the fact that you'll be without your "new" guitar until the repair gets done. I just don't get people sometimes. |
|