Author |
Message |
elwoodblue
Senior Member Username: elwoodblue
Post Number: 1798 Registered: 6-2002
| Posted on Monday, January 18, 2016 - 3:18 am: |  |
A thing I've made recently,from parts hanging around the shop.It's a successful study of simplicity, with a bit of improv I gotta say thanks to Alembic for small (and large) inspirations that will no doubt show up in my creations. Like this ;)
The body is limba, and is the 'waste' portion of trimming a slab for another guitar body. That's why it's reversed (long horn on bottom). I tried to make a straight cut through the slab with a looong sawzall blade.I made a guide frame with metal runners on each side...and but for one episode of the blade veering out, it worked. Those few seconds where the blade path went wonky is the cause of the massive hollow in the back (sanded out to a nice contour). It's pretty crazy how thin it must be under the bass side of the bridge.It does great things for the sound....and if I ever get a belly...it should hang nicely. The neck is an old dimarzio that I roasted in the oven for a while.The guitar is maybe 4 lbs as is. I'm thinking one alumitone or lipstick pickup at the neck and one volume knob...to keep things light. Here's some more pics...
Next up...something totally different~
(Message edited by elwoodblue on January 18, 2016) |
sonicus
Senior Member Username: sonicus
Post Number: 4711 Registered: 5-2009
| Posted on Monday, January 18, 2016 - 3:34 am: |  |
The above pics look interesting . I await and look forward to the creation of a new kind of critter . Wolf |
elwoodblue
Senior Member Username: elwoodblue
Post Number: 1799 Registered: 6-2002
| Posted on Monday, January 18, 2016 - 4:04 am: |  |
Here's a better teaser then, I'll sit down and load more pics after I make some more wood dusts
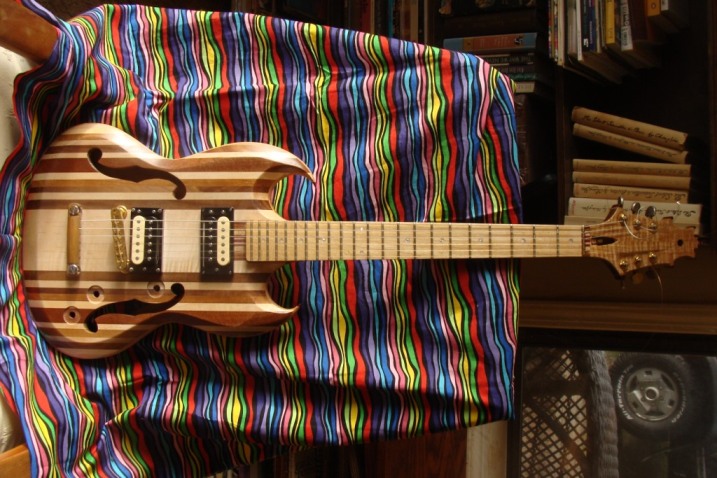 |
benson_murrensun
Senior Member Username: benson_murrensun
Post Number: 651 Registered: 5-2007
| Posted on Monday, January 18, 2016 - 7:55 am: |  |
A semi-hollow SG - I don't thin I've ever seen such a thing. It looks great! I would be concerned about it being neck-heavy, though. Is it? |
elwoodblue
Senior Member Username: elwoodblue
Post Number: 1800 Registered: 6-2002
| Posted on Monday, January 18, 2016 - 8:20 am: |  |
Thanks Benson, I guess I won't really know until the guts are in and the strap buttons on. The body has some substance, being walnut and maple, I hope that will help.I could always stash a brass slide in there ;). |
benson_murrensun
Senior Member Username: benson_murrensun
Post Number: 652 Registered: 5-2007
| Posted on Wednesday, January 20, 2016 - 7:23 am: |  |
Yeah, or some lead shot. Anyway, nice job! |
edwardofhuncote
Senior Member Username: edwardofhuncote
Post Number: 786 Registered: 6-2014
| Posted on Wednesday, January 20, 2016 - 8:33 am: |  |
Nice work Elwood! Is this a set-neck or neck-through? Was just thinking I could really use your expertise on a project I just thunk up the other day. FYI - I had a short nightmare about using a sawz-all for a rip-cut the other night after reading your first post... Man, don't scare me like that! |
elwoodblue
Senior Member Username: elwoodblue
Post Number: 1802 Registered: 6-2002
| Posted on Wednesday, January 20, 2016 - 1:28 pm: |  |
Thanks Edward. It's a mega set neck; along with the wood to wood joints, I embedded a 4" x 1/2" steel dowel between the neck and body . The neck is an early 80's gibson V2 neck,I added maple/walnut veneers then the fingerboard.And headstock veneers and nubs. It is much more interesting than the simple gibson cone shape I started with. I did have to improvise when I realized the headstock was now too thick to fit the tuners.I'm happy with the results and it's good practice for the same situation on the 7 string I have in the works. I'll make a new nut that will just barely keep the string splay from spilling over. I think I got the neck angle right,but I guess the extra veneers and maybe the fret height brought the string plane up a tad. The stock bridge studs I had for the bridge were too short, so I found some bolts with same threads and they enter through the back.The string tension holds everything tight and it's easy to adjust and lock it down with the wheel and nut on top.I might add more nuts on the studs (with loctite to prevent resonance)if I find that keeps energy in the strings. The neck joint I see as hippy 'club' sandwich...walnut,maple,purpleheart,mango...bring thoughts of rye,sourdough,tomato,etc. You might think the maple at the rear of the heel has stress cracks,the lines are spalting that just ended up that way. I ran two wires up the neck for a backlit design, they are now in a bit of hard glue in the cavity (I didn't really protect them from overflow when glueing the top veneer).I might be able to unbind them,if not...sigh,then next time!!.) I also need to reconfigure the lower horn(..that's what she said!), it's a little stabby. The pickups are from an '81 sonex (only good thing about those beasts unless you need an ineffective sledgehammer ). Here are some pics, sanding sealer only for now so things might not pop like we know it will when it's done.
edward,whatcha working on ? elwood |
edwardofhuncote
Senior Member Username: edwardofhuncote
Post Number: 790 Registered: 6-2014
| Posted on Thursday, January 21, 2016 - 7:17 am: |  |
Just a crazy idea right now... it's a fretless Tobias 5-string currently routed for J-type pickups. Would love to find a set of Alembic activators, wired Vol/Pan/Filter for it, but if that doesn't come along in a timely fashion, I may end up installing a set of Bartolini electronics. They were taken out of a brand-new Lakland 55-01, and as I understand it, are wired with a three-band tone circuit with a Master Volume and Pan. In short, I can handle the wood stuff, but wires and soldering scare me... that's where you come in. =) PS, I like the way you've recessed the top for the knobs here. |
elwoodblue
Senior Member Username: elwoodblue
Post Number: 1804 Registered: 6-2002
| Posted on Thursday, January 21, 2016 - 8:45 pm: |  |
The Barts sound like a good idea, especially if you could just trade out everything for the Alembic set when it shows up.Just let me know when your ready,I can probably help. I'm in the same boat on my next build, but I might end up with EMG's for the time being. I have this double bass that is about 10 years old. I bought it for 750 so I know it's gotta be a bit of a dog, but maybe there are some things I can do to make it better (like checking to see if the post is just right). I'm even thinking of coating the finger board with something hard(it appears to be a black stained white wood). The bridge appears to be seated well but I can check and do the sandpaper thing if it's off. Any other thoughts come to mind?I am a newbie to this old tech I'll take some pics soon. |
edwardofhuncote
Senior Member Username: edwardofhuncote
Post Number: 803 Registered: 6-2014
| Posted on Wednesday, January 27, 2016 - 12:45 pm: |  |
Gimme' til this evening and I'll give a more detailed post... hadn't seen this one until you call attention to it. |
edwardofhuncote
Senior Member Username: edwardofhuncote
Post Number: 804 Registered: 6-2014
| Posted on Wednesday, January 27, 2016 - 4:38 pm: |  |
Elwood, regarding soundpost location, there is no one definite spot for it, however there's a zone where the best spot could be. In most cases, it's about one square inch. First step, make sure your bridge is where it should be. There are little notches on the f-holes for alignment, think of them as timing marks. Generally speaking, the back of the bridge should line up with the lower ones when the bridge is standing perfectly vertical. When fitted correctly the back of the bridge is perpendicular to the top, whereas the front looks like it's leaning back towards the tailpiece. (I think there's a picture of this on one of my threads) On bridge location, there's no hard and fast answer here... scale lengths vary between instruments, but generally a 3/4-size bass should be about 42" give or take a couple fractions. Once the bridge is located, my general practice is to start with the soundpost positioned so the the *center* of the top of it is about 1-1/4" below the *center* of the bridge's treble foot. Make sure it is standing perfectly vertical. (observe closely, because with it standing between two arched surfaces, there's an optical illusion) Once you've got it there, tune up to pitch and play a little. Take note of any dead or weak notes or any wolf notes. De-tune slightly, more on the G and D strings, and move the soundpost North or South a quarter-inch, and tune back up. Is it different, better, worse? Hint - moving the soundpost closer to the bridge foot will dampen bass response but increase treble response. Likewise in reverse. Another thing to keep in mind, because the top and bsck are arched, the soundpost will tighten as you pull it toward the treble f-hole, and loosen as you pushn it toward the center of the top. Keep the post in the same centerline with the bridge foot. A little bit either way won't hurt anything, but stay in bounds. Chances are, moving the soundpost won't make a huge difference on an all-laminated bass, provided it's cline anyway, but it definitely will matter. In my experience, the fit and quality of the post is more detrimental. Too tight, and it will just kill a bass, too loose and they fall out or the top collapses. You can't believe how many broom-handle soundposts I've removed. More than a couple of them were either glued or nailed in. Yes, *nailed*. I found one screwed in one time. Cousin Cletus even took extra time to counter sink the screws. And the basses they came out of just sounded awful. Use only a good spruce dowel. Simple, no substitutes acceptable. You will have to have a soundpost setter for this. https://internationalviolin.com/ProductDetail/t81_sound-post-setter-bass One of these is a darn good idea too. https://internationalviolin.com/ProductDetail/t915_bass-soundpost-retriever On your fingerboard; (this is an easy one) Just get a good ol' rattle-can of black enamel. Buy the good stuff, shake well, apply evenly to a well prepared surface. Cure for a couple days, then wet-sand and polish to a dull luster. (because glossy shows every imperfection) Yeah, it'll wear off again one day, but it's a $5 fix. If you're confident enough to remove the "ebonized" maple board, (and I have no trouble thinking you are) I highly recommend replacing it with Jatoba, sometimes called Brazilian Cherry. It's dirt cheap, hard as any rosewood, and dresses out to a nice orange-brown. (Englehardt uses it now instead of rosewood) While you're at it, take the finish off the playing surface of the neck. If I'm right, your bass is either a Cremona or Palatino-branded import, with a huge neck. Feel free to rasp that thing down to a reasonable profile. Sorry to throw so much information at you... email me anytime at my addy here for more specific thoughts. |
elwoodblue
Senior Member Username: elwoodblue
Post Number: 1810 Registered: 6-2002
| Posted on Wednesday, January 27, 2016 - 5:27 pm: |  |
Great stuff, thanks! I think the post is dead center under the treble foot, probably contributing to the lack of bass response. I'll get some pics up soon,so you can see the how things are now. How about action? Is it a trade-off for punchiness (higher action=more punch)? I cut the nut slots low for playability. That brought the bridge slots down a lot, but I figured the bridge was just slapped on there for the sales floor and was never dialed in further. Thanks for the license to rasp...that could be fun  |
edwardofhuncote
Senior Member Username: edwardofhuncote
Post Number: 806 Registered: 6-2014
| Posted on Thursday, January 28, 2016 - 6:30 am: |  |
Oh yeah, if the soundpost is directly underneath the bridge foot, that'll squelch the bass response. And if the bridge gets a hard enough impact, it'll punch the soundpost right through the back. Seen that twice now, both on new basses that came out of the shipping box that way. I measure the string height at the end of the fingerboard. For medium action, there should be about 7-9mm clearance on the G, and 10-12mm for the E. Again, these measurements are just a guideline... Just in general, for higher tension steel strings I will go lower at the bridge, for lower tension "slap" strings, higher to allow for more travel. (I am a great big wuss when it comes to high action... upright basses are hard enough to play as it is!) =) At risk of overstating the obvious, no two basses ever feel the same, even if they measure the same. So many other variables, probably the biggest being neck relief. I'm guessing your bass has very little relief with that chunky neck. 3/32 - 1/8" is pretty normal, much more than that starts making it hard to play outside first position. Also, take into account how much upward "sweep" is in the fingerboard extension. It's really a game of compromise. Yeah, you'll give up a little volume with lower action, but the trade off is that the bass is waaaay easier to play. I'm plugged-in 90% of the time I'm on upright anyway, so it doesn't matter much. Hope that helps. |
elwoodblue
Senior Member Username: elwoodblue
Post Number: 1813 Registered: 6-2002
| Posted on Sunday, January 31, 2016 - 6:04 am: |  |
A whole step forward, a half step back... I made some progress,then I broke a string...doh! The soundpost is now about an inch behind the bridge, I can tell the difference. Now there is warmth to the notes, and the resonance feeds back into the strings for a little bloom. I had to move the bridge a hair to match the f-hole notches,it now needs reseating. There is some noticeable gaps under the feet. Since I lowered the action before, any sanding will bring the bridge too low. If I glue some hardwood laminates to the feet to raise the bridge will that add resistance to the energy tranfer? ...or will it make it better? I have never seen a stand-up bridge made of laminates, is it like the soundpost that it's best made from one piece of light porous tight grained wood? I'm going to see if I can get the A string back on for the experiments, I better start saving for a new set. These are only 7-8 years old but they haven't seen enough use and I think all the new attention was too much ahh...tension.(sorry) If hippy sandwich feet won't fly, I'll have to make a new bridge. I'm open to buying one...but this is a wood thread. I have a small bandsaw, but no jigsaw (but I'm a whiz at coping!!). What do you think? Wow...there's a new instrument in the house now...and it's been here all along! thanks for the help,it's working I saw this the other day, now I know what the fingerboard for the SHG above was slated for. So that build has a Marauder fingerboard,Sonex pickups, and a V2 neck...keeping well with the butcher block/barber stripe theme where if it doesn't match...it fits. (Message edited by elwoodblue on January 31, 2016) |
edwardofhuncote
Senior Member Username: edwardofhuncote
Post Number: 810 Registered: 6-2014
| Posted on Monday, February 01, 2016 - 5:46 am: |  |
Elwood, you can get by with shimming bridge feet if done correctly, in fact, I have some shims I'll be glad to send you. They are actually the pieces leftover whenever a new bridge is cut... I save them just for this reason. (this way, the grain is already oriented the right direction, and they are roughly the right size) Just hit my email addy here if you need some. I use industrial CA glue for sticking the shims on the feet. After which, a couple passes over the belt sander, and some careful trimming with a Dremel tool will flush everything up. FWIW - I have made new bridges, but it's waaaay more trouble than it's worth. If you decide to go that route, you can buy a new bridge blank for $35, give or take. Glad to help! |
elwoodblue
Senior Member Username: elwoodblue
Post Number: 1830 Registered: 6-2002
| Posted on Friday, February 19, 2016 - 12:49 am: |  |
I've got the stand up in the wood room...after looking at a bunch of neck profiles I'm realizing how huge these import necks are. I'll take some pics of the reshaping for kicks. Here's a nice side project, This is a G&L prototype ASAT bass that didn't make to production. I love the look, but was wondering about the pickup placement. The Lynx,El Toro,and Interceptor basses all have a bridge and middle but nothing close to the neck. Or angled like the middle pup here:
So I made a testbed bass in the spirit of Leo's testbeds (like the one in the printout).
I used some reclaimed mahogany from an old pool table,with some black walnut blocks and a 90's 3 bolt SB-2 neck. It's tight but woody with alot of warmth,but not too much woof. ...and it's light! I'd almost consider playing gigs with it.Here's a side view: I've got the fretboard for my 7 string finished, I need to decide on pickups so I can proceed with the routing. The neck pup will be angled so I'll use an 8 string pup with a 7 string at the bridge. I'm thinking a EMG 707 (and 808) wouldn't be terrible.Any other pickup ideas for an extended range 7 string (29 3/8" scale)?(...barts,etc.) I'll try and get some progress pics up soon. |
hankster
Senior Member Username: hankster
Post Number: 431 Registered: 6-2004
| Posted on Friday, February 19, 2016 - 7:08 pm: |  |
Great! Has an appealing Flintstones vibe. That's a compliment, by the way! |
elwoodblue
Senior Member Username: elwoodblue
Post Number: 1844 Registered: 6-2002
| Posted on Wednesday, March 02, 2016 - 3:28 am: |  |
Late night upright update: I think I'm understanding the term CCB better. I recarved the neck,it's not a 2x4 anymore but it still feels big.Good enough for now. I sanded the tarry black paint off the fingerboard, it looks like oakish Ash, or maybe ashish Oak. I clearcoated it and went to work on the bridge. I used some Mangofor feet lams that seemed similar in grain density and direction. Since it's a plywood top I figured this was just another ply above the top. Sanded the feet with the sandpaper inverted on the top, ...fished the post out and got all the strings almost to tension. I spent a little time playing with post placement, but I think now the plywood top and back is the tone limiting factor now. I bet if the top wasn't plywood I would get more punch and detail across the frequencies. I'm going to have to sand the tongue down on the E side alot too...it's not close to straight. So that's how I've come to understand my CCB better. I bet it's nice playing one made the right way Thanks again for the guidance,it's been fun wrangling that beast if just for practice. |
edwardofhuncote
Senior Member Username: edwardofhuncote
Post Number: 867 Registered: 6-2014
| Posted on Wednesday, March 02, 2016 - 3:56 am: |  |
Sounds like you're headed the right way Elwood. =) I just started on another top-off restoration of an old 1940's Kay. I may chronicle that one or not... it's nothing special, kinda' has that so-ugly-it's-cute puppy appeal. A friend of mine (get this) a completely blind since birth piano repairman, bought it for $200. Bass bar was out, hence the tell-tale collapsed top. It's got all the right components to be a great player though, and (being blind) the owner has no reason to care what it *looks* like. |
elwoodblue
Senior Member Username: elwoodblue
Post Number: 1845 Registered: 6-2002
| Posted on Wednesday, March 02, 2016 - 4:55 am: |  |
A while back while selling a bass on ebay,I kept getting an message asking for a person to person phone call. I thought it strange, I mean...why not type the question? I talked to the guy for 20 minutes about basses before he told me he was blind. I can't remember the band ,but he was a player in the Motown times. My bass(Lado Superhawk) had some finish checking etc. and he was looking for an instrument that 'felt' good. The brass bling and pretty lacewood wasn't a selling point in that case . One thing about that conversation that I really enjoyed; He said even though it had been years since he driven a car, he'd still dream about rolling down the road! ;) |
elwoodblue
Senior Member Username: elwoodblue
Post Number: 1846 Registered: 6-2002
| Posted on Wednesday, March 02, 2016 - 4:56 am: |  |
A while back while selling a bass on ebay,I kept getting an message asking for a person to person phone call. I thought it strange, I mean...why not type the question? I talked to the guy for 20 minutes about basses before he told me he was blind. I can't remember the band ,but he was a player in the Motown times. My bass(Lado SuperFalcon) had some finish checking etc. and he was looking for an instrument that 'felt' good. The brass bling and pretty lacewood wasn't a selling point in that case . One thing about that conversation that I really enjoyed; He said even though it had been years since he driven a car, he'd still dream about rolling down the road! ;) |
elwoodblue
Senior Member Username: elwoodblue
Post Number: 1847 Registered: 6-2002
| Posted on Wednesday, March 02, 2016 - 4:58 am: |  |
A while back while selling a bass on ebay,I kept getting an message asking for a person to person phone call. I thought it strange, I mean...why not type the question? I talked to the guy for 20 minutes about basses before he told me he was blind. I can't remember the band ,but he was a player in the Motown times. My bass(Lado SuperFalcon) had some finish checking etc. and he was looking for an instrument that 'felt' good. The brass bling and pretty lacewood wasn't a selling point in that case . One thing about that conversation that I really enjoyed; He said even though it had been years since he had driven a car, he'd still dream about rolling down the road! ;) |
elwoodblue
Senior Member Username: elwoodblue
Post Number: 1868 Registered: 6-2002
| Posted on Saturday, March 26, 2016 - 8:33 pm: |  |
A few pics of my 7 string progress: Here's proof of elbow grease-
Form and function got a little cozy at the end-
Fretted and glued to the neck. Showing the Hipshot tuners I decided to try-
A teaser body shot-
The body is a single piece of Mango. That's some nice chatoyance there-
I'm going to cap the tailpiece with some cocobolo. Wood is so cool ;)
There's alot of work to do still...
It's crazy how much time I've spent,because it's a one-off and I've had to improvise while adapting to the designs and shaping I did 20 years ago when I bought the wood. I'd say there's still 5-10 hours more;gotta finish the tailpiece,make a bridge,make a nut,final carvings,finish ,fretwork,install pups etc... ...maybe 20 hours? I swear I AM getting better at time management...LOL. |
edwardofhuncote
Senior Member Username: edwardofhuncote
Post Number: 899 Registered: 6-2014
| Posted on Sunday, March 27, 2016 - 7:03 am: |  |
I LIKE IT! Hey, do you guys have Woodcrafter's stores out there? I don't know if they're nation-wide or not. I can't get out of a wood store for less than $100 anymore... |
|