Author |
Message |
mica
Moderator Username: mica
Post Number: 2373 Registered: 6-2000
| Posted on Thursday, March 31, 2005 - 1:55 pm: |  |
Picking up the converation from the woodbank, here's that #3766 with the Small Standard body shape outlined. |
mica
Moderator Username: mica
Post Number: 2374 Registered: 6-2000
| Posted on Thursday, March 31, 2005 - 1:57 pm: |  |
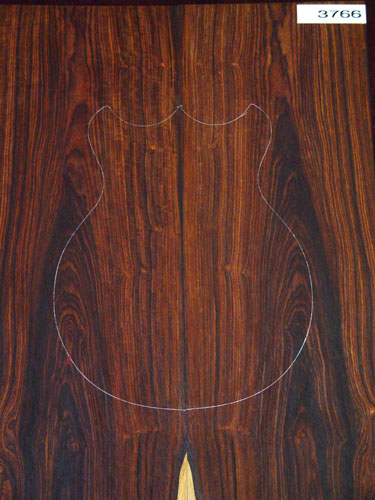 |
bsee
Senior Member Username: bsee
Post Number: 812 Registered: 3-2004
| Posted on Thursday, March 31, 2005 - 4:46 pm: |  |
Thanks Mica! I really needed to see the body lines on there for an approximate scale. While the photos had the inch lines there for scale, I just couldn't picture the scale of the body shape to apply it. I appreciate that this position captures the eyes in the dark part of the wood, but how about something more like the photoshop hack I am putting in here? I think the four little eyes in a row are cool, and I thought the best feature of this wood was the figuring in the light section near the top center. I can be swayed either way, so I would appreciate any comments from others who may stop by the thread as well! Thanks! Here's the pic:
|
valvil
Moderator Username: valvil
Post Number: 676 Registered: 7-2002
| Posted on Thursday, March 31, 2005 - 5:32 pm: |  |
Hello Bob, yes, we can position it that way too, no problem. As soon as you decide which way you want to go we can begin construction. Valentino |
bsee
Senior Member Username: bsee
Post Number: 813 Registered: 3-2004
| Posted on Thursday, March 31, 2005 - 6:58 pm: |  |
Mica/Valentino, this all looks great! Thanks! I think we're about there for the top wood, I'd just like to leave it open for a day or so in case anyone has an interesting comment. Relative to the build order, there are a few things that I am not 100% comfortable with at this point: 1. We need to select a back wood. I am leaning toward either 3767 or 3774. I really like the light/dark/light stripes abutting the sap wood on 3767 and think that would work well with the colors of the PH and ebony in the neck. This one probably is most similar to the top. Otherwise, a reversal of the bookmatch on 3774 would provide for the body contour to approximately follow the rings and create that natural sunburst effect. Anyone have an opinion? I suspect that 3767 with a high placement on the board and cut at the very edge of the sap wood is the likely winner here as it will be the most organic combination with the top. 2. I'd like an extremely dark headstock laminate to really offset the gold H/W and silver logo, preferably something that looks symmetrical. In particular, I'd be looking for blacks and reds with limited orange. I think the orange would take away from the contrast/impact of the gold pegs. 3. Also, on the headstock, what woods will the intermediate laminates be? You ususally don't use cocobolo for this, right? What do you think of an eb/map/ph/map/eb plywood to match the neck laminates (and body sandwich) to the bevel and provide that really dark face? I'd still love a dark cocobolo face in place of the ebony there, but let me know what is feasible and what you think would work best. 4. The original spec had the neck pickup moved a bit toward the neck, though there isn't room to move it much. I want to make sure I can get plenty of bottom out of this thing. The 4R is still the "full-sized" truss rod cover, right? I am open to guidance on this matter, particularly if the High Wizard has an opinion. 5. I believe that I confirmed this before, but the brass backplates are gold plated, correct? 6. I'd like to be careful about the position of the LED toggle relative to the jack. I tend to use 90 degree cables and hook the lead between the strap and the bass as a strain relief, but it hangs free if I am playing seated. I just want to make sure I don't toggle it by accident, or worse, break it. The control layout from Randy's Custom Clarke Deluxe would be great, but I didn't spec in the side jack. What do you recommend? 7. Also with the LEDs, there's a dimmer pot inside the control cavity? Thanks again, I am so excited to get the production process underway! -Bob |
bsee
Senior Member Username: bsee
Post Number: 814 Registered: 3-2004
| Posted on Thursday, March 31, 2005 - 7:39 pm: |  |
Oh, and one last thing... If there is any variation available in the neck laminates, I would like the non-maple lams to be at the thick end of the spectrum. Is there one standard for these, or is there some poetic license from neck to neck? The lams on my '90 Persuader seem fairly beefy at just about 1/4" each. Also, they wouldn't all have to be the same thickness. I think it would look really interesting if the ebony center lam were slightly thicker than the ones beside it. I think an ideal would be something like 3/8 or 5/16 for the center ebony, 3/16 or 1/8 for the inner maples, and then 1/4 for the PH lams. 1/4" per lam will work just great, too, and I'm probably making this a bit too complicated. If there's a standard, or if the customization here would be inconvenient or a burden, then I will just go with whatever works for you. |
palembic
Senior Member Username: palembic
Post Number: 1972 Registered: 9-2002
| Posted on Thursday, March 31, 2005 - 11:01 pm: |  |
Hi Bob and friends, When seeing this outline of the bass on the wood I wonder if it wouldn't be nice to leave the "parallel lines" concept of the topwood and go for putting the both pieces bookmatch to center in an "angle", so the more "chevron" style, like this: >>>. You have to leave out a triangle part from the bottom-up. A triangle that could be recuperated in the peghead I guess?? Or in a box??? HA! Paul the bad one
|
bsee
Senior Member Username: bsee
Post Number: 816 Registered: 3-2004
| Posted on Thursday, March 31, 2005 - 11:57 pm: |  |
Hi Paul- Thanks for the thoughts. I played with that possibility myself because I really like the chevron affect. The selected position isn't so much about parallel lines, it's more that there's just some really cool figuring in the center area near the top that I don't wish to give up. Also, I couldn't get happy with the mix of dark and light and the way the instrument flowed with any of my attempts to lay out a chevron. I would say, also, that I didn't spring for book-to-center. I think this would be a tough wood choice for going to center in balancing the dark and light effects. Also, the pickups and electronics would go over the nifty figuring. Thanks for making me think about this! The more I look at this, the more I am pleased by it. I would just want to confirm my photoshop hack with another chalk outline whenever that would be convenient. In particular, I'd be looking at the position of the dark section on the upper wing. Still looking for thoughts on the back wood and the placement of pickups and controls, though! Thanks, Paul! -Bob |
jacko
Intermediate Member Username: jacko
Post Number: 141 Registered: 10-2002
| Posted on Friday, April 01, 2005 - 2:55 am: |  |
hi Bob. Good to see you're finally getting your custom. Have you thought about turning the wood the other way up and swapping sides so the lighter angled figuring (coming down from the 3766 number) is going up the body. this would give a pretty cool chevron effect but would lose the figuring you like. In the end, It's your choice so take your time. My preference is for the swirly patterns. Good look with this one. Graeme |
bsee
Senior Member Username: bsee
Post Number: 817 Registered: 3-2004
| Posted on Friday, April 01, 2005 - 6:49 am: |  |
Hi Graeme- Yes, that is something I played with in Photoshop as well. I do like the interesting grain pattern where it opens up above the dark areas, but the dark areas were still a part of the instrument on the upper wing, and I didn't think the way they ended up fitting in looked as organic. If the board was cut to extend another six inches or so up above the cutoff point, it might have worked, but who knows what would have been going on in the wood up there? I also wondered about the back side of these boards, but I've put these guys through enough hassles and the bookmatch of the wood is likely to be pretty different there. I really like swirly patterns, too. If I were to have my choice of all the wood ever listed, there are a couple selections from the sold pieces and one or two from the currently available Tribute boards that I really like. On the other hand, since I am trying to build a "poor man's" version of the SC 30th anniversary bass here, I think this wood comes fairly close to capturing that feel. I really expect this wood to become alive once finished. Thanks for the thoughts! -Bob |
davehouck
Moderator Username: davehouck
Post Number: 1569 Registered: 5-2002
| Posted on Friday, April 01, 2005 - 7:17 am: |  |
Hi Bob; my first thought too was the chevron approach. But it looks like you've thought that through. Also, I was assuming you were bookmatching to center, and the chevron approach isn't as effective if not going to center. |
bsee
Senior Member Username: bsee
Post Number: 818 Registered: 3-2004
| Posted on Friday, April 01, 2005 - 7:26 am: |  |
Being a neurotic, I went back over the emails that I had sent over the past few months as well as the discussions pre-order. There are four more items beyond what was already posted. If we call the neck laminates width question #8, then: 9. Bridge block? I thought it was specified as having one in the order but don't see that represented on your spec sheet. I was asking for guidance on this item, so maybe someone decided I would be better off without it for the tone I am looking for? 10. The crown headstock shape. Originally, we were talking about a K-crown or a crown that was narrower at the bottom than the top. The latter was a consideration to better adapt to the narrow nut width. I think this detail got lost in the order spec, but let me know which crown variant you think will best fit with the rest of the design. 11. Neck dimensions. You sepcified it as 1.5 x 2.25. Is that "actual nut width" x "bridge string spacing"? Just confirming here, I think that's what you're saying. In the catalogs, the necks are specified by the nut and 24th fret widths, and I think that 2.25 at the 24th would be way too wide. Could you confirm the actual measurements of the SC 30th bass? 12. Someone had said they were getting their straplocks mounted with bolts into inserts. I asked about this as well since I have always had problems with straplock screws backing themselves out. Looking back to the earlier issues, I think 3767 will be "it" for the back wood if it is still available. Can I ask for a pic of it with the body outline drawn in pushed toward the top of the wood and omitting most or all of the sapwood? This would have to be slightly canted to follow the line of that light/dark/light stripe. The stripe isn't perfectly straight, but I am looking to keep as little sapwood as possible without losing the integrity of the lines. Thanks again!
|
flaxattack
Senior Member Username: flaxattack
Post Number: 425 Registered: 4-2004
| Posted on Saturday, April 02, 2005 - 7:18 pm: |  |
looks awesome- you got the "flax" neck!!! lol >heres 2 cents >go for the continous wood back plates >it imho looks so much better and you have so much invested already- pls >think about it,.,,,,its gonna be less than 400 >compare it with some with brass photos >yes i know no one sees the back.... >but i am kinda weird-i love the backs of alembics- maybe cause its just >more wood and less stuff >ask them to show you the back woods >oh and on the top wood photo >i tend to lean to chips.. >reason >all your controls can be slide down a little or will be inside the darker area by itself with none of or few of the lines being covered- also chips has more of a v shape >did u play with moving it down? >to right above the pinch in the center >that might be good too >tis goona be sweet whatever way
|
bsee
Senior Member Username: bsee
Post Number: 832 Registered: 3-2004
| Posted on Saturday, April 02, 2005 - 7:48 pm: |  |
Thanks, Jeff! I do agree on the wood backplates. I wish I took that option. I think the frugal in me didn't want to pay the full upcharge for gold plating, which includes the backplates, and then pay again to replace those with wood. Oddly, I would definitely have taken the option if I were leaving the brass alone. I'll ask if they'll let me make that change and what the cost will be, especially with the nice back wood. Regarding the body position, I see your point. I considered a number of possibilities there; up, down, canted in, canted out, even the same set of variations upside down. I am really betting all my chips that the flame-looking areas in the center of the board are going to come forward and deepen with time and a finish. If I am wrong, I'll have a very nice bass. If I am lucky, then it will be incredible. Thanks again! -Bob |
bob
Advanced Member Username: bob
Post Number: 388 Registered: 11-2002
| Posted on Saturday, April 02, 2005 - 9:21 pm: |  |
Bob, get real: these people are not going to charge you for gold-plating some pieces of brass, throwing them away, and then building you a completely new set of continuous wood plates. Go for it. |
bsee
Senior Member Username: bsee
Post Number: 833 Registered: 3-2004
| Posted on Saturday, April 02, 2005 - 9:48 pm: |  |
Bob, Certainly they wouldn't go through the trouble of making the plates and paying for them to be plated if the order is changed to continuous wood. I honestly don't know what they would charge under the circumstances, but the details from the configurator don't drill down to that level of detail. I didn't ask when I was making the order, I had enough other details to work out and it was the hectic end-of-year rush when the order was going in. I was too busy waffling on more serious details at the time, like scale length and number of strings! As you can see from the thread, there are even more details that seemed worked out at the time but aren't entirely clear. It's always better to ask than assume, so this will get figured out over the next week or two with everything else... As much detail as we're getting into before the build, the only surprise I want when this bass gets delivered is how much better it looks in person than in photos. I can't wait to see the abalone! I just love the swirls and colors in that shell.
|
bob
Advanced Member Username: bob
Post Number: 389 Registered: 11-2002
| Posted on Sunday, April 03, 2005 - 1:00 am: |  |
Bob, I know. If you like, someday I'll email you my own list of details, some of which just fell off the list. And at the other extreme, there is nothing like that first glimpse of the real thing, or even a small part of it. Though the wait will be difficult, I think you're really in the most stressful part of the process right now. It's actually starting, there's a sense of urgency to nail down every last detail... yet you somehow have to balance that with the magic of the whole thing. And it's very easy to let certain details - like the number you get out of a fairly simple quote generator - distract you from the important stuff. I just thought it was worth reminding you that you're working with real human beings here, and artists at that (though I know you understand that). You've waited a long time for this, so take a deep breath, maybe even call a time out for a week or so just to regroup. A few extra days at this point won't matter at all a year from now, and as I'm sure you realize, everyone - most especially you - will be happier if you wait until it all feels right, rather than questioning and changing things during the build, or second-guessing what you end up with. On a related note, I think we've discussed your "frugal" nature in the past, and I respect that. Don't know if this will help any, but by the time I finally paid the balance on mine, I found I was already into next year's discretionary spending. Still don't think I really wanted LEDs, but looking back on it now the cost should not have been given as much weight as it was. It doesn't seem to me that you're one of the people who is going to do a whole series of customs, so take the time to get it right. And lots of slow, deep breaths. |
bsee
Senior Member Username: bsee
Post Number: 834 Registered: 3-2004
| Posted on Sunday, April 03, 2005 - 5:44 am: |  |
I think we're on the same page, Bob. Making changes once the build actually starts is a definite no-no. There's too much chance of missing things or making a change that isn't going to flow with the whole design. Also, I paid in full for my instrument up front (by bank check, so no loss of a couple percent to the credit card people). Answering all of my questions and making design tweaks is enough hardship for any dealer without going out-of-pocket for a couple months while waiting for delivery. You do what you can. Once production starts, I'll just sit back and take what updates I get until it shows up on my doorstep. The only way I'll be saying anything is if I see something in photos that doesn't match the spec, or if they ask. Honestly, the wait doesn't bother me at all. If the backplates get added, then there will be only one option that I wanted and passed on, getting the logo done "with shell". Did I mention how much I love abalone? |
flaxattack
Senior Member Username: flaxattack
Post Number: 428 Registered: 4-2004
| Posted on Sunday, April 03, 2005 - 8:36 am: |  |
i will bet you $1 that you WILL make a change during production-lmao definitely sit back and relax- close your eyes, go into a coma and wake up 6 months from now |
jacko
Intermediate Member Username: jacko
Post Number: 142 Registered: 10-2002
| Posted on Monday, April 04, 2005 - 1:17 am: |  |
Bob. One thing I can guarantee is how much better your bass will be in person than in the Photos. When i opened my case for the first time I just sat and stared for ages;-) i agree with the other bob here, if your going for a back laminate, continuous wood backplates are a must. graeme |
flaxattack
Senior Member Username: flaxattack
Post Number: 436 Registered: 4-2004
| Posted on Monday, April 04, 2005 - 6:44 am: |  |
bob trust me they will not dfo the brass plating till months from now and will make the change if you wish get the continous |
bsee
Senior Member Username: bsee
Post Number: 840 Registered: 3-2004
| Posted on Monday, April 04, 2005 - 11:25 am: |  |
Ok, here's to summarize the discussion in one place for the benefit of all: Top wood: 3766 in approximately the position I identified. Adjustment criteria would include: -optimal positioning of the little eyes -angle and coverage of the dark areas on the body wings -will there be dark stripes along the sides of the neck, or is that dark just an illusion from the cut? If so, should they be trimmed out? 1. Back wood: 3767 positioned near the top of the board and slightly canted to eliminate most or all of the sap wood. Looking to have the light/dark/light stripes abut the neck. Please show me a pic with templates when convenient. 2/3/10. Headstock: Looking for a very dark and symmetrical face to set off the hardware and logo. Looking to confirm the laminates for the headstock as they will be apparent with the bevel. Looking to get the right crown variation to best flow with the overall design. 4. Need to confirm the pickup placement. 5. Are the brass backplates to be goldplated? This could be trumped by a change to wood backplates at the urging of others in the know. If this change would be allowed, can I get a price including, if appropriate, any reduction in the price of the gold plating? I will let Beaver know I am asking since you will probably want to feed that to me through him. 6. Looking for ideas on control positions, particularly related to the LED toggle and the output jack. I don't want to break/trigger the toggle with my cable. 7. Is there a dimmer for the LEDs inside the cavity? 8. I would like the non-maple laminates in the neck at the wide end of the spectrum if there is any room for variation here. 9. Bridge block: I think it was in the original spec but I don't see it mentioned on the build sheet. I am not sure I fully understand it to know if I even want one. Please guide me... 11. Confirming what your definition of the neck measurements means. Looking for the SC 30th neck, though maybe a hair wider, especially if you believe it is necessary to maintain neck stability in a New England climate and with regular strings. 12. Can/will the straplocks be mounted using threaded inserts? Valentino/Mica- You may have my office number, but I have been out of work there since 3/1. I will email you my cell phone number in case you don't have it so that we can discuss any of this directly and at your convenience, as you see fit. Thanks to all who have participated so far, and to any who may yet choose to chime in! -Bob PS - Jeff, once production starts, I refuse to make any change that isn't directly in response to a query from Alembic. |
kilowatt
New Username: kilowatt
Post Number: 9 Registered: 12-2004
| Posted on Monday, April 04, 2005 - 1:33 pm: |  |
Bob, I am also in line to have a 5 string MK with series II electronics built. I have LED's going in and am having a three position switch and a dimmer. The switch will be, all on,side on, and all off. You can talk to Beaver on this as my bass is also going through Bass Central. Don't feel too bad about making changes at this stage of the build, they are much easier to deal with now. I am still trying to decide on inlays and continuous wood backplates myself. Pete |
bsee
Senior Member Username: bsee
Post Number: 841 Registered: 3-2004
| Posted on Monday, April 04, 2005 - 1:50 pm: |  |
Pete- With regard to inlays, you may have gathered that I am a big fan of abalone. I really love the colors and the lines, making them much more interesting to me than MOP. I am not familiar enough with the other options to say. I suppose that an "inlay materials" page would be a great addition to the site so that one could examine all the common materials. You can see the guidance that others have provided regarding the backplates. Having already paid my bass off in full, it seems easier to find a couple hundred to throw at them now than it would have to push the original total up when I was placing the order. With regard to the LEDs, I have side only. I had heard that there is a dimmer placed inside the control cavity so that you could adjust how bright they are when they come on. With front LEDs, particularly if you went laser, you might want a more readily accessible dimmer to control their brightness, but that's not what I am talking about here. I think the perfect side LED setup would be a 3-way switch allowing for {off / on low / on high}, but an internal dimmer is better than just on/off. Oddly, the darker the room, the less bright the LEDs need to be. Thanks for the feedback, and good luck with your bass! -Bob |
bob
Advanced Member Username: bob
Post Number: 391 Registered: 11-2002
| Posted on Monday, April 04, 2005 - 7:10 pm: |  |
Hey Bob, have you considered abalone? |
bsee
Senior Member Username: bsee
Post Number: 842 Registered: 3-2004
| Posted on Monday, April 04, 2005 - 7:32 pm: |  |
Interesting concept, Bob. I believe that I have thought long and hard on the subject of abalone. The only thing that would turn me on as much as more abalone would be more cowbell. Unfortunately, I am not sure where I can fit more abalone into the design. Maybe abalone pickup covers? Maybe I should have asked about the cool abalone caps they put on Stanley's control knobs? -Bob
|
jacko
Intermediate Member Username: jacko
Post Number: 144 Registered: 10-2002
| Posted on Tuesday, April 05, 2005 - 3:38 am: |  |
hey bob. Just my two-pennorth. I think the dark edges alongside the neck would look pretty cool and highlight the maple nicely. no 6. As the LEDs are going to be on or off, put the switch well out of the way - perhaps even on the lower horn - it's not one of the controls you're gong to be playing with during a gig. graeme |
bsee
Senior Member Username: bsee
Post Number: 844 Registered: 3-2004
| Posted on Tuesday, April 05, 2005 - 5:49 am: |  |
Graeme- I think it would be a lot of work to put one mini-toggle out on the lower horn. I also think that a mini-toggle out there alone would be a bit silly looking. I suppose another alternative might be to use a mini-pot type switch instead of a toggle. Something like what they use for the pickup selector seems like it would be more sturdy and harder to have an accident with. I will wait, though, to see what Alembic recommends on the matter. There's always the issue of how things fit in the control cavity, so it has to go someplace where there is space for it. Thanks! -Bob |
jacko
Intermediate Member Username: jacko
Post Number: 145 Registered: 10-2002
| Posted on Tuesday, April 05, 2005 - 5:52 am: |  |
Yep, That was probably a bit extreme but the suggestion still stands. How about tucked below the rest of the controls (looking down whilst playing that is) graeme |
bsee
Senior Member Username: bsee
Post Number: 845 Registered: 3-2004
| Posted on Tuesday, April 05, 2005 - 6:02 am: |  |
That would be a possibility as long as it isn't close enough to the edge that it would get a thigh-tap while playing seated. Worse yet, it might get caught on a loose pair of pants in the same playing situation, and that could be pretty ugly. I'm trying to avoid all of the bad design characteristics I have experienced during 30 years of playing. When all is said and done, the side jack is probably the easiest option (least hassle, most straightforward, easiest to describe) for Alembic to execute on. We'll find out soon... -Bob |
|