|
This is Eric, he is prepping an instrument for another coat of finish to be applied. On our high gloss finish instruments, a coat of spray is applied, left to cure for 24 hours, then sanded down and sprayed again. This process continues until all the pores of he wood grain have been filled and have enough coating to be sanded and buffed to a high gloss. This is a subjective process and each instrument determines how much finish will be needed to complete the task. Some instruments require only 10-15 coats of finish, while others like coco-bolo or the burl woods require as much as 25 coats. Remember, we use no fillers to cloud the depth of the grain on our woods. |
 |
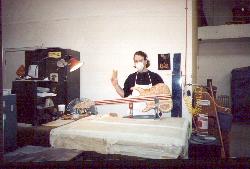 |
|
|
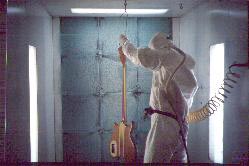 |
 |
It's not an Intel guy, it's Eric in the spray booth! You will notice he looks like he is outfitted for a trip into space. Well that's sort of true. He is entering a different kind of space where the air quality is not conducive to normal breathing activities, nor would the overspray do much for his clothing. Although OSHA requires only a respirator mask for this job function, we feel that you can't adequately get a good seal with one given the different contours of a face not to mention the possibility of mustaches and beards making a good seal impossible. We choose the space suit method with a fresh air line so he is always supplied with clean air and no part of his body or clothing is exposed. The suit has another added bonus, no small hairs or filaments of clothing can float into the wet finish. Making our finishes we feel the cleanest in the industry. |
|
|
This is our drying room. The instruments need to dry completely between each coat of spray and then they are sanded and sprayed again. |
 |
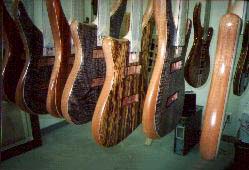 |
|
|
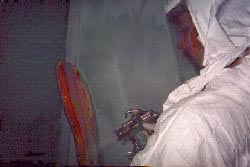 |
 |
Applying finish to the body of a bass. |
|
|
Applying finish to the neck of a bass. |
 |
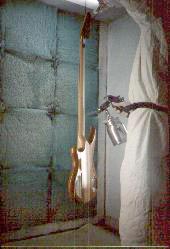 |
|
|
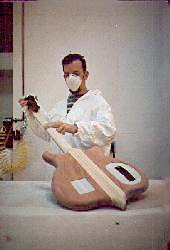 |
 |
Eric is feeling the back of the neck to make sure there is a smooth surface and no runs before applying another coat of finish to this Mark King Standard model. Any runs that may have occurred in the previous coat of finish must be sanded smooth before applying another coat. |
|
|
This is a beautiful coco-bolo Essence bass. It has reached the desired density of finish and is now being prep sanded for the two part buffing it will receive to achieve the high gloss finish this model is known for. |
 |
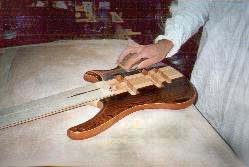 |
|
|
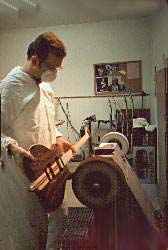 |
 |
Eric has determined that this Series I instrument is now ready for buffing. The finish has a look that we call "orange peel". It looks very much like the surface of an orange. The object is to achieve a glass like surface on the instrument, to achieve this is a multi step process. We begin by using varying grits of sandpaper to obtain a smooth surface. This is always done in the same direction of the wood grain. The scratches in the surface this creates are incredibly fine and now will be buffed out in two parts. You see the buffing station is outfitted with two wheels. One is coated with a red rouge and the instrument is buffed all over, then he will switch to the white rouge wheel for the final gloss buffing. The instrument will now be inspected and move into the set-up room. |
|